Steer-by-Wire
Force Feedback Actuator Hybrid Solution
Software-defined vehicles will require new types of actuators whose features and functions will be enabled primarily by software.
INVENTUS is developing the world’s smallest steer-by-wire force feedback actuator with the best performance and cost, based on its leading-edge technology:
Magnetorheological (MR) media actuator.
A small electric motor combined with a powerful MR brake not only provides the desired steering feel (haptic) and quick response, but also ensures robust end-stop torque capability and much higher functional safety. The system is characterized by minimal space requirements, lower costs, higher performance, safety and reliability.
We are now looking for partners to bring this groundbreaking steer-by-wire technology to mass production and the market.
Inventus' steer-by-wire brake offers several advantages:
The combination of a small electric motor and a powerful MR brake (magnetorheological brake) = Hybrid Direct Drive (HDD) enables a very compact design with very low energy consumption. This saves space, costs and weight in the vehicle.
By integrating this technology (Hybrid-Direct-Drive), vehicle manufacturers can save approximately 20 Euros on the steer-by-wire handwheel actuator and an additional 10 Euros on the control unit. 1 Nm of braking torque with an MR brake costs € 0.60; with an electric motor, it costs € 6.00 .
The Hybrid Direct Drive solution requires much less installation space than the state of the art and thus offers more flexibility in design, as it is suitable for head-up displays, retractable steering wheels, left- and right-hand drive vehicles. This enables standardization of the steering column for different vehicle types (standardized steering column).
The MR-Brake can efficiently generate a braking torque of up to 35 Nm, enabling precise and reliable feedback at the steering wheel (end stops; Steering wheel grip for entry and exit; wheels on curb).
The combination of a small electric motor and an MR brake with high efficiency ensures excellent thermal heat management, which increases the longevity and reliability of the
State of the art steer-by-wire force feedback actuator:
Generation 1
The belt-driven steer-by-wire force-feedback actuator of the Tesla Cybertruck is state of the art.
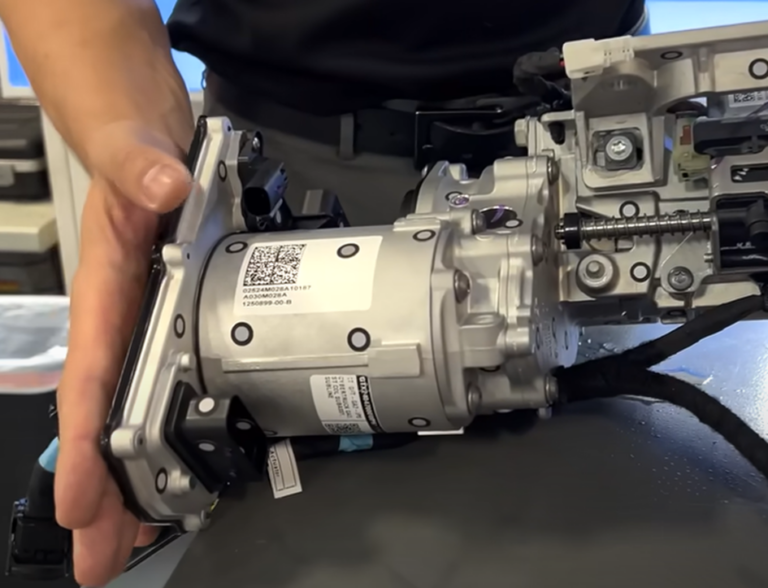
Using a drive motor for braking, especially at very low speeds or even at standstill, is very inefficient because the electric motor requires high currents and mainly generates power losses (heat).
Overriding the drive motor with additional mechanical components such as a gearbox or belt does not change much (a 25 Nm end stop is static), but it degrades the feel, creates backlash and increases complexity and susceptibility to failure.
This is why vehicles brake with disc/friction brakes and use a power-off parking brake for over 100 years, because they are efficient, simple, proven, cost effective and powerful.
At the time of the Steer-by-Wire Force-Feedback Actuator (SbW FFA) Generation 1, only the combination of an electric motor and a reduction gear / belt drive was technologically feasible and could be implemented in series production.
The Inventus Hybrid-Direct-Drive with a small electric motor and a powerful MR brake now enables the consistent technical implementation of the requirements without any disadvantages or compromises = SbW FFA Generation 2.
We asked ourselves the question: Why should the force feedback torque required for the steering wheel (e.g. 25 Nm) be transmitted at least 500 mm into the cockpit interior via complex sliding shafts (for stowable steering columns with more than 150 or 250 mm travel and even double telescopic shafts), bearings and support structures in order to generate the counter-torque?
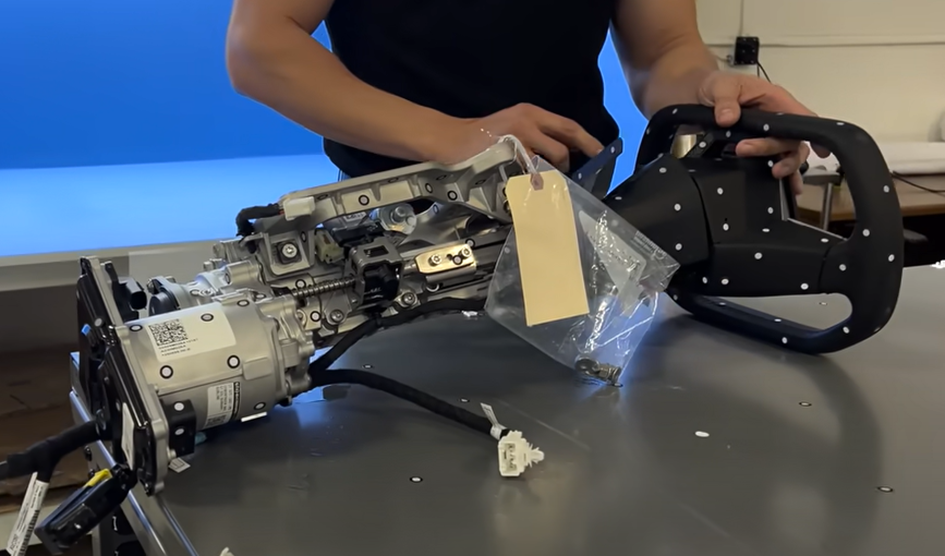
It is much easier to process the torque directly and immediately where it is generated, at the steering wheel. However, this is only possible if the force feedback actuator is (very) compact, not too heavy and does not require too much power (due to the power cable cross sections, which would otherwise affect the length and height adjustment).
INVENTUS Hybrid-Direct-Drive (HDD):
Generation 2
The combination of a high-torque MR brake and a small electric motor provides much more design freedom, the generation 2 of Steer-by-Wire force feedback actuator.
Symmetrical body –> left or right-hand drive vehicles with the same system.
This makes the standardized steering column possible (one for all).
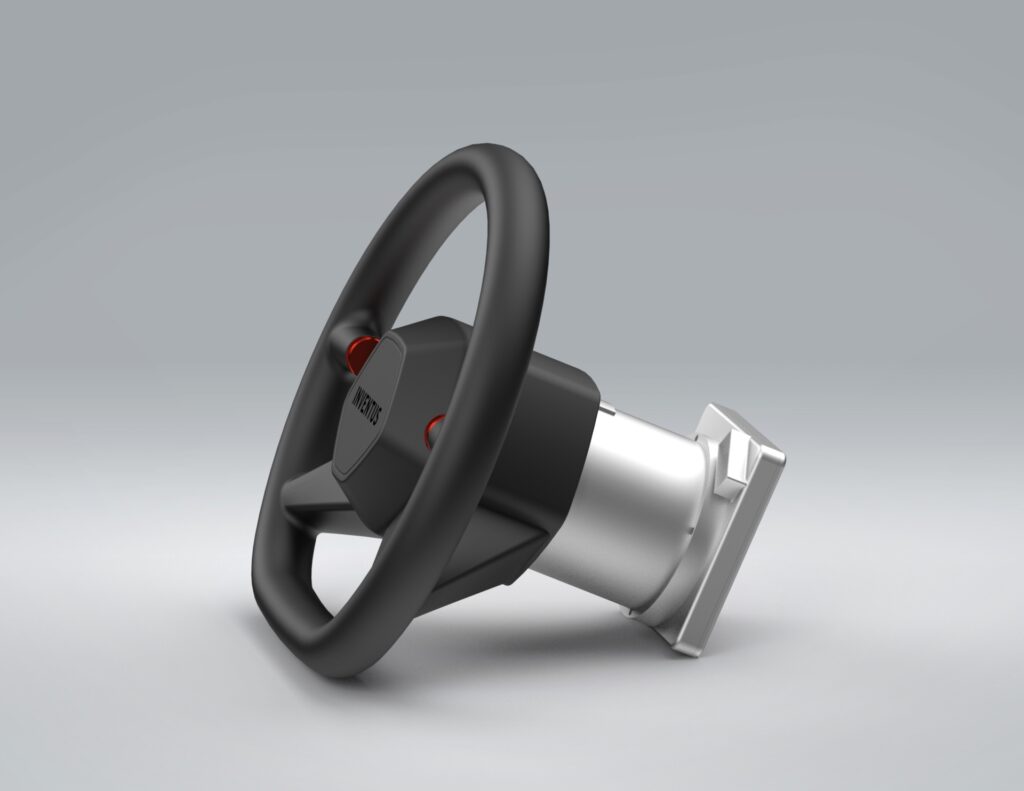
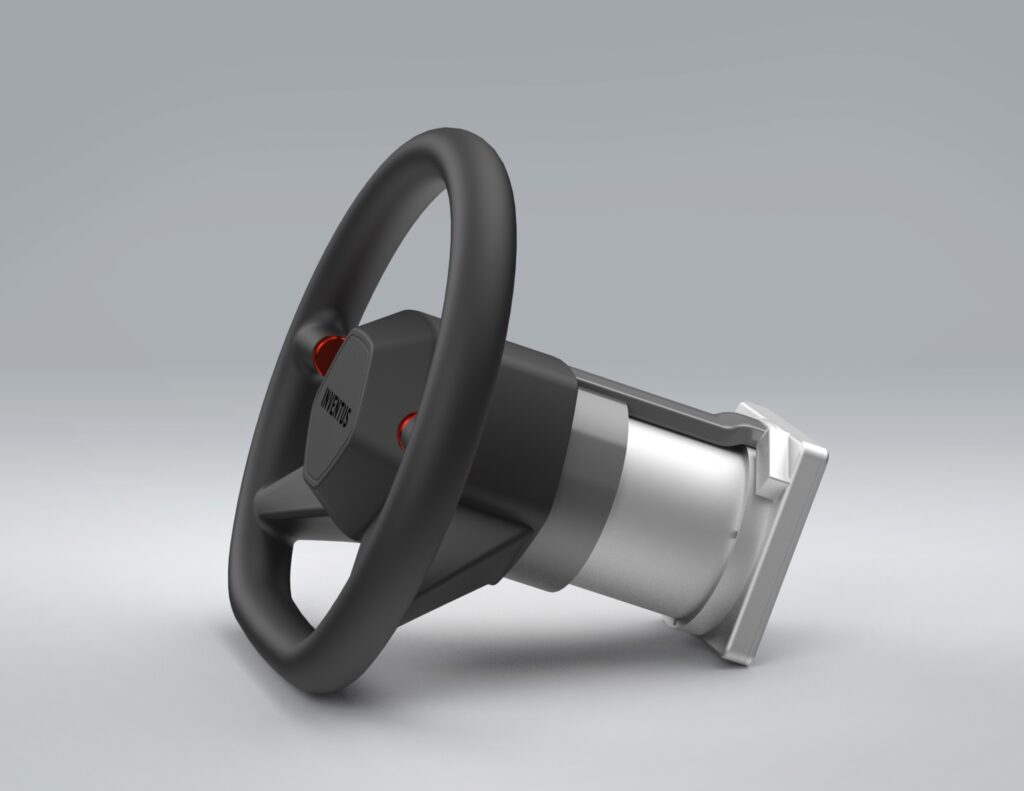
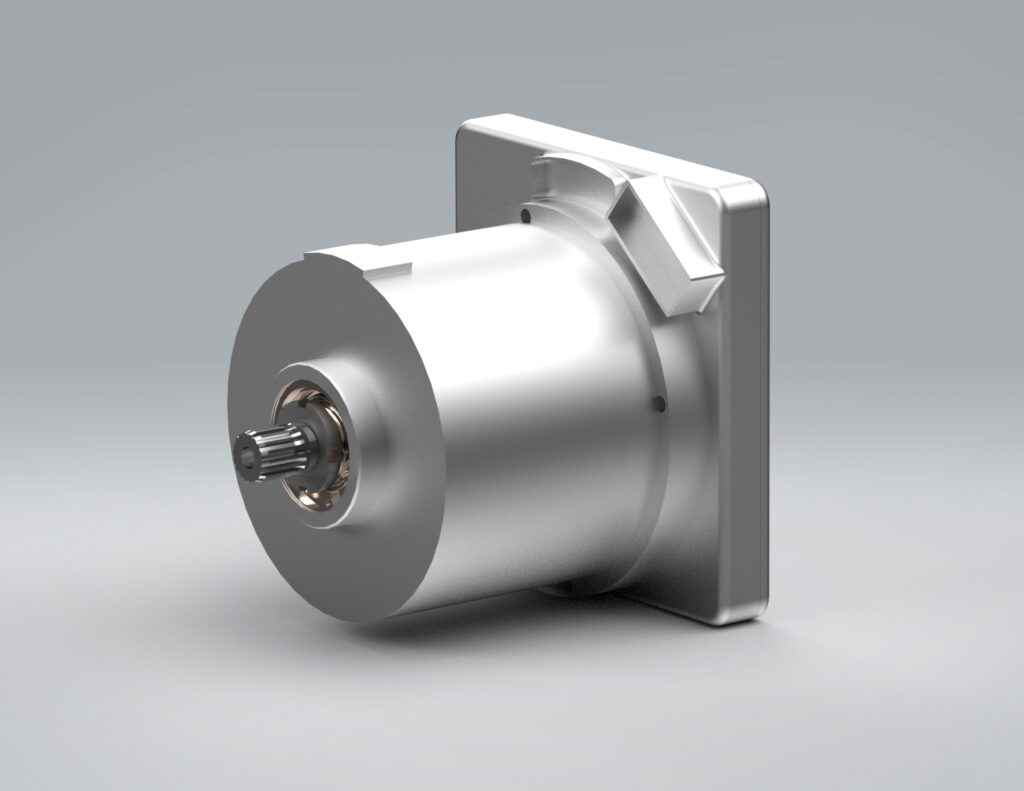
Our combination of MR brake and electric motor (HDD) makes this solution possible: We call this Steer-by-Wire Force-Feedback-Actuator installation close to the steering wheel. The car manufacturer saves about €20 per SbW FFA unit compared to the state of the art, plus about €10 in ECU costs (where these savings come from is described in detail further down on the website). Here are three examples of what this can look like:
Actuator installation close to steering wheel

Option 1: MR brake + E-motor + Internal Electronic
(max. ± 170° rotation range)
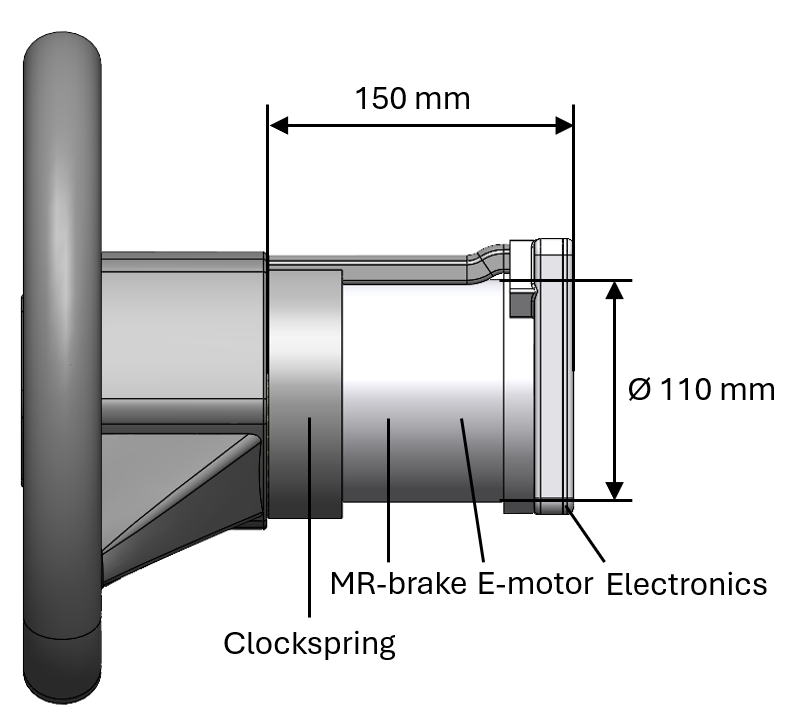
Option 2: MR brake + E-motor + Clockspring
(same roatition range as clockspring)
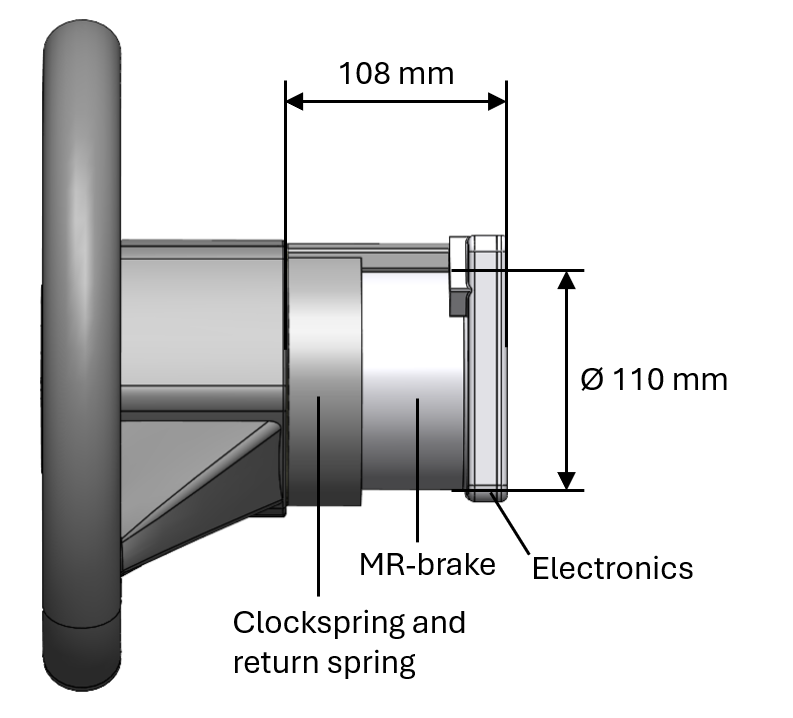
Option 3: MR brake + Returnspring + Clockspring
(same roatition range as clockspring)
Of course, we have also taken into account the length and height adjustment, crash absorption and cable routing. We are happy to show this to you after you have signed an NDA with us.
A well-known car manufacturer said to us, after we had presented our direct drive close to the steering wheel solution: „The suppliers always offer us their old technical solutions, so that they can empty their parts shelves. We want the best technical solution, because your solution is also cheaper: “INVENTUS build us a working model of your next generation Force-Feedback-Actuator”.
INVENTUS doesn’t have to sell (technically outdated) serial parts, we supply the (best) technology.
The INVENTUS Steer-by-Wire Force Feedback Actuator (SbW FFA) hybrid solution combines a small e-motor (e.g. max. 6 Nm) with a powerful yet compact MR-brake (25 to 35 Nm) and thus provides the world’s smallest SbW system combining extraordinary performance, excellent thermal management and cost advantages.
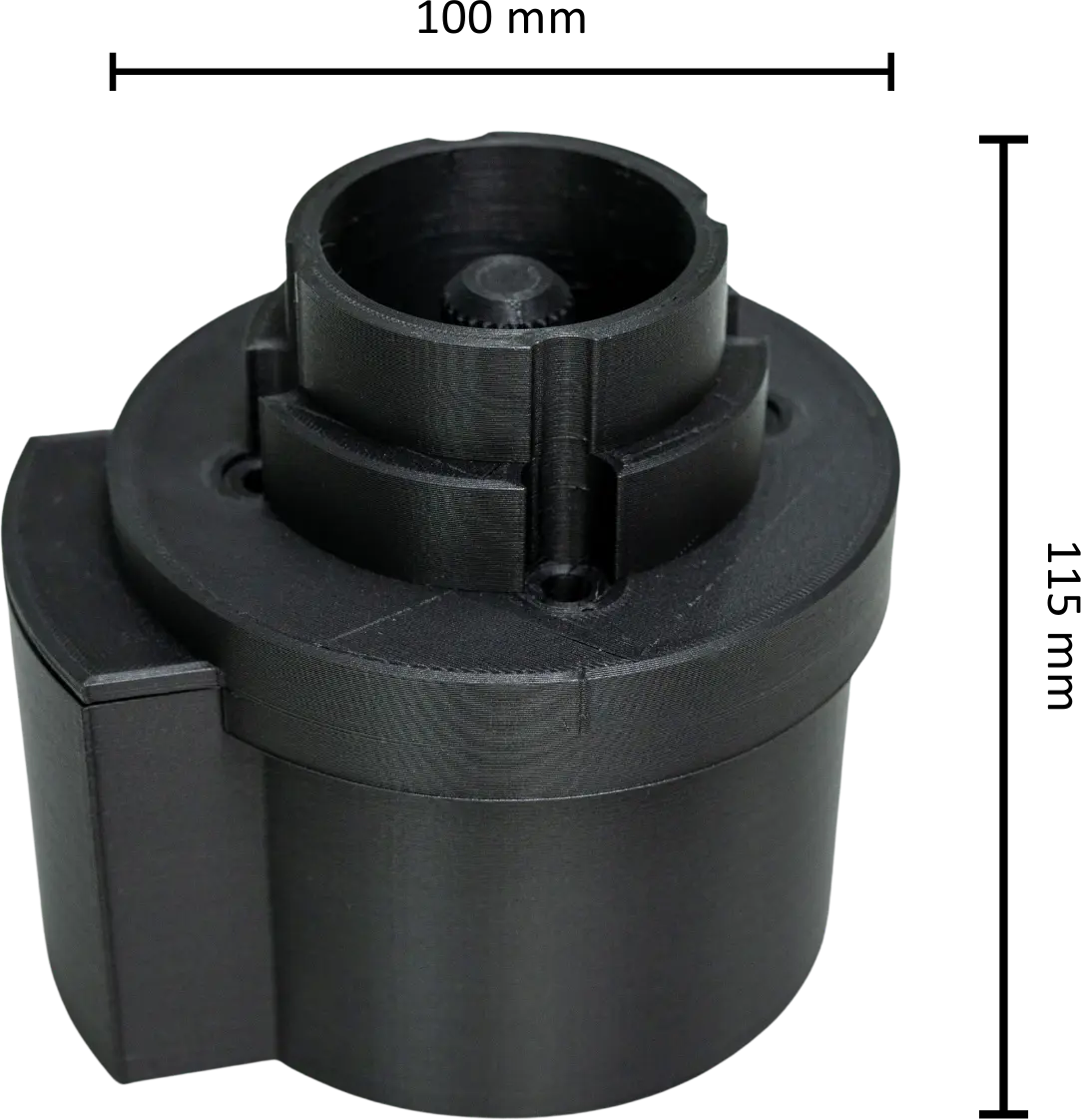
Key Features
Compact
design
Thanks to our patented MR brake, we can significantly reduce the size of the active component (factor 3-7) and thus the overall system size.
Reliable and
fail-safe&
Safety first is our guiding design principle. That’s why our hybrid system offers two options for safe operation in case of an emergency.
Intuitive steering
Our hybrid steer-by-wire solution generates strong force feedback (active & braking force) for intuitive and safe steering maneuvers.
Highly
cost efficient
The use of a significantly smaller active component and the optimization of the entire system result in cost savings in the double-digit euro range.
Thermal management
The INVENTUS SbW system features particularly efficient heat management, ensuring the entire system to remain cool at all times.
There is no ideal solution – not yet
Current SbW technologies are based on Column Electric Power Steering, Direct Drive, and Belt Drive systems at a number of positions at the steering column or steering wheel.
While driving in SbW mode, the force feedback experienced by the driver consists of about 80% braking torque (up to 35 Nm) and active feedback of 6-8 Nm (about 20%).
While all systems mentioned above can generate a high degree of active feedback, it is the high degree of braking performance for which state-of-the-art SbW systems are not optimized. This results in target conflicts regarding:
- the haptic/force feedback (sufficient basic torque with absence of backlash, ripples, and cogging torque…)
- the required installation space
- the warm-up time and
- the overall system weight
To address this challenge, we combine our years of experience in MR technologies and our high-performance braking systems with the advantages of active steering systems.
Our solution: The world’s smallest SbW system with extraordinary performance and efficiency for increased cost advantages.

INVENTUS steer-by-wire solution
INVENTUS MR brake technology
- We make use of our patented MR brake technology with a basic torque of <0.1 Nm.
- Due to the low base torque, the sensitivity of the steering system can be tailored to any customers requirements.
- The MR brake torque changes within milliseconds with an extremely very low power consumption of 4.2 amps / 60 watts (at 12 volts) to generate 25 Nm in <10 ms.
- A torque sensor is not mandatory.
INVENTUS hybrid steer-by-wire system
- Our MR brakes are extremely efficient in generating the required passive torques.
- This way, we can reduce the size of the electric motor for active torque generation by a factor of 3 to 7.
- Combining the advantages of both technologies we provide a smaller, stronger and more efficient SbW solution.
INVENTUS SbW FFA Hybrid Solution
INVENTUS Steer-by-Wire steering column Hybrid-Direct-Drive (HDD) setup
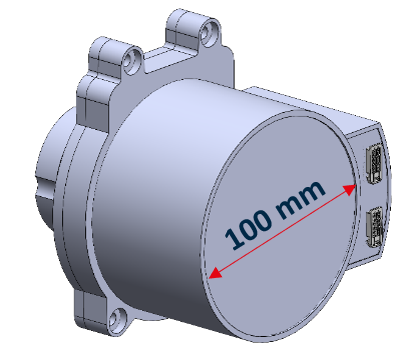
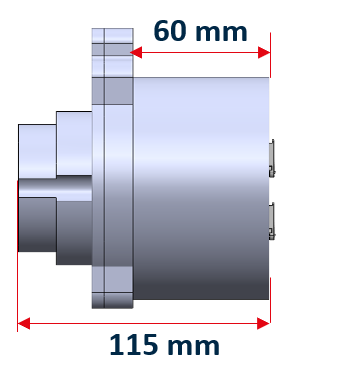
Passive torque generation (MR brake) of 25 Nm
Active torque generation (electric motor) of 5 Nm
Also applicable for Hybrid Belt Drive (HBD) or Hybrid Worm Drive (HWD) solutions
Size comparison between electric motor solutions
and the INVENTUS MR brake technology
INVENTUS hybrid steer-by-wire system
Steering torque of up to 25 Nm
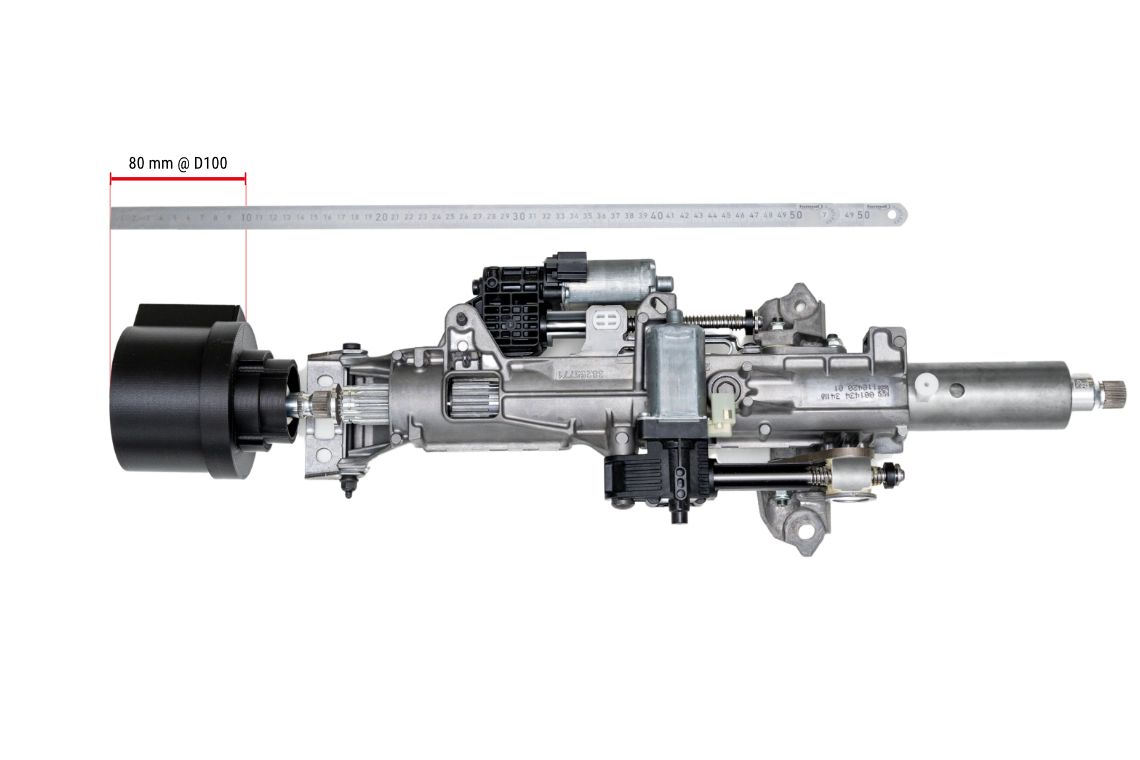
DDA steer-by-wire system using an electric motor
Steering torque of up to 25 Nm
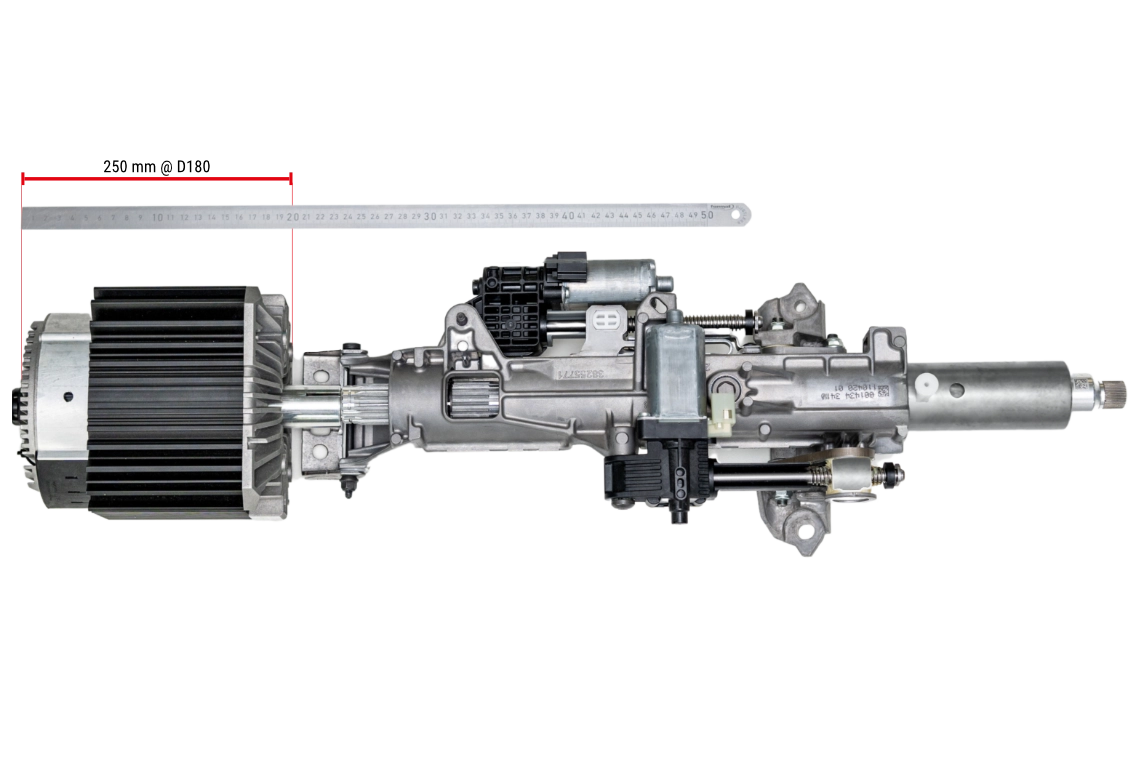
Electric motor VS INVENTUS MR brake
5 Nm
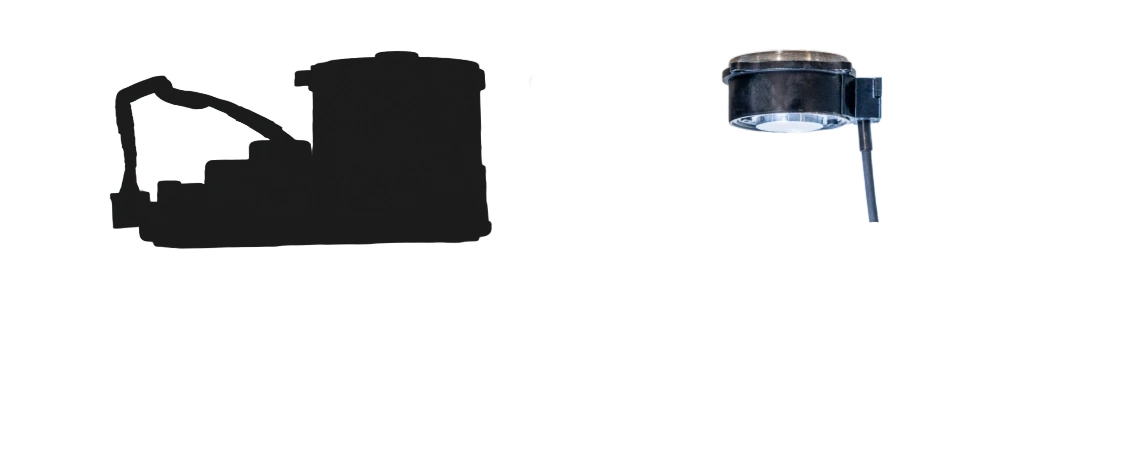
Compared to several electric motors, the INVENTUS system’s symmetrical design on the steering column is another advantage.
INVENTUS MR brake VS Electric motor
25 Nm
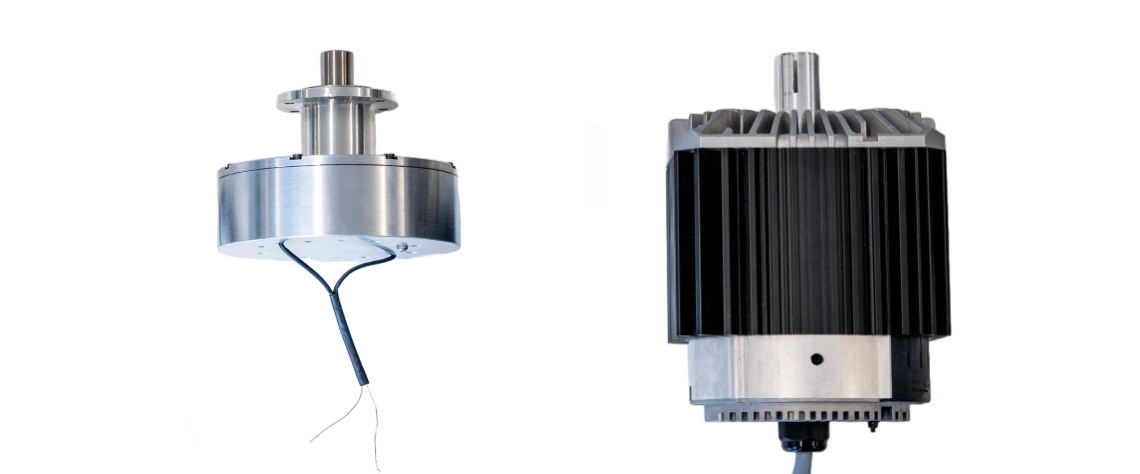
INVENTUS MR brake operating principle
The basic design of our INVENTUS MR brake is quite simple.
How it works
- The brake consists of a rotor, a stator, an electric coil, as well as bearings and seals
- The gap between the rotor and the stator is filled with carbonyl iron powder (MRP – magnetorheological powder)
- As soon as a current is applied to the coil, a magnetic field is generated, which closes from the rotor via the active gap to the stator
- The magnetic field in the effective gap/between the surfaces moving towards each other, causes the carbonyl iron particles to build „magnetic particle bridges“, generating shear stresses
- The forces resulting from the shear stresses, multiplied by the distance, produce a torque (braking torque)
- The electric coil can be attached to either the rotor or the stator. The shaft or the housing can rotate
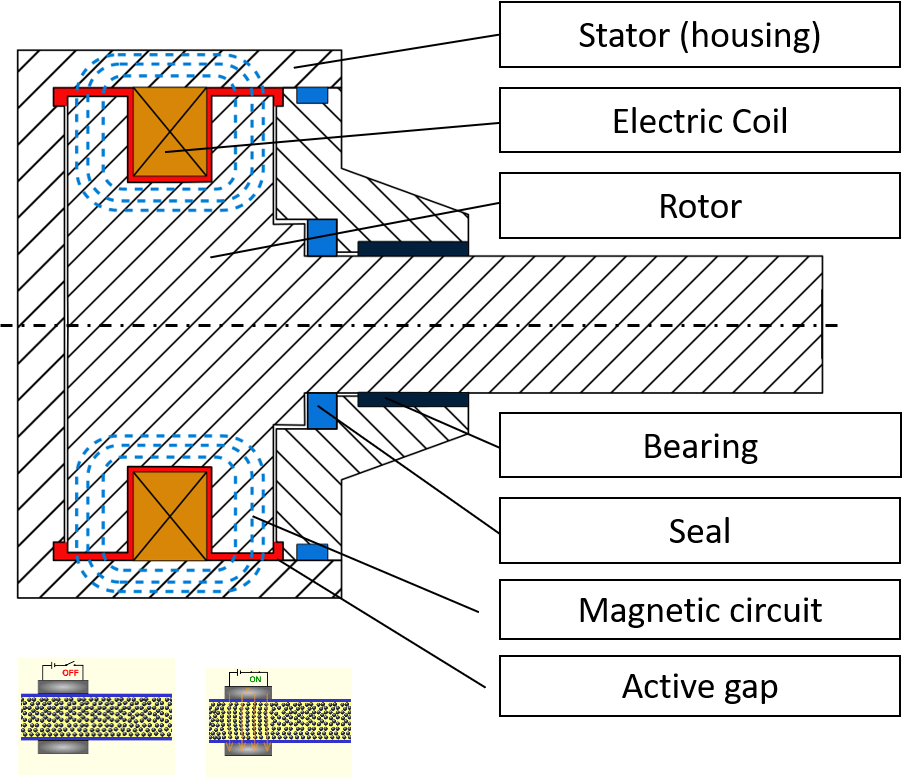
INVENTUS SbW hybrid system
force feedback performance
State of the art solutions
In normal driving operation, >80% of the steering movements are passive torques as most maneuvers are quasi-static or very slow twists. State of the art solutions generate torque with a redundant electric motor, usually with transmission (gear, belt…). However, at low speeds and high torque requirements, electric motors have an extremely high electrical power loss, making them highly inefficient.
Force feedback requirements for intuitive and reliable steering operations
- Steering wheel torque in normal driving mode = 1 to 3 Nm
- Maximum torque = 25 to 35 Nm (e.g., end stop, egress or holding on to steering wheel)
- Maximum reset torque = 5 to 8 Nm
- Maximum angular velocity = approx. 1400 °/sec (evasive maneuvers)
- Up to 35 Nm braking torque / passive torque
(braking steering movement/torque generated by the driver) - Up to 8 Nm active torque generation
(active rotation of the steering wheel, e.g., after a U-turn)
INVENTUS SbW FFA hybrid solution active & passive steering torque
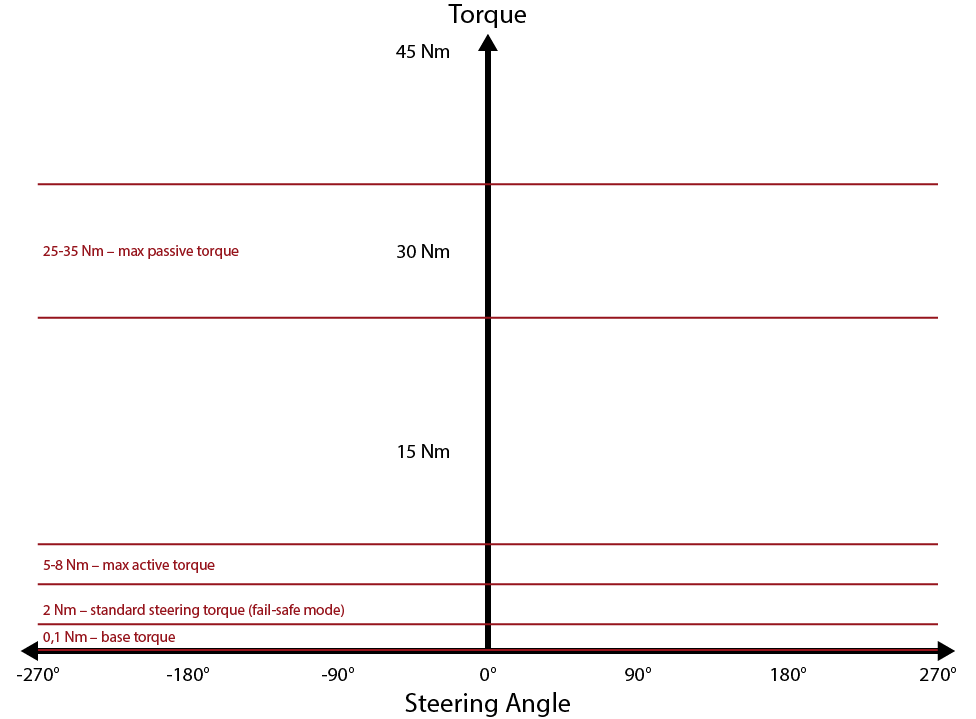
Examples of adaptive braking curves
The INVENTUS SbW hybrid system can change the braking behavior and thus the perceptible steering behavior in real time.
Also, watch the videos below to experience the adaptive force feedback of our system.
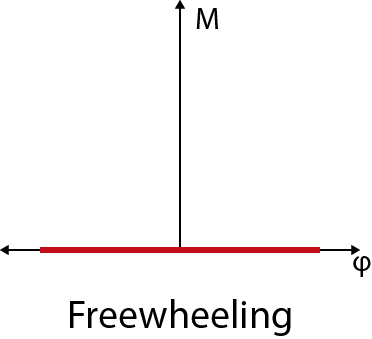
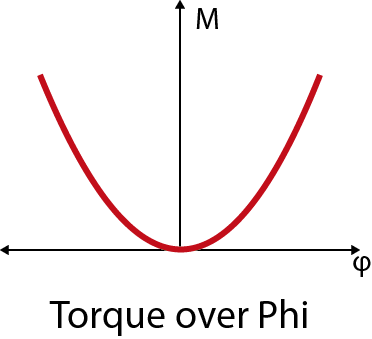
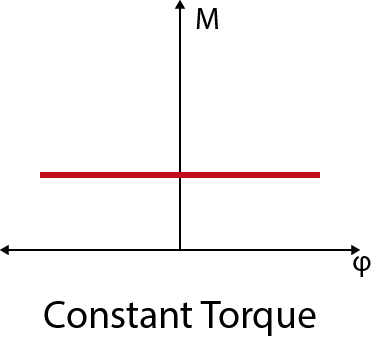
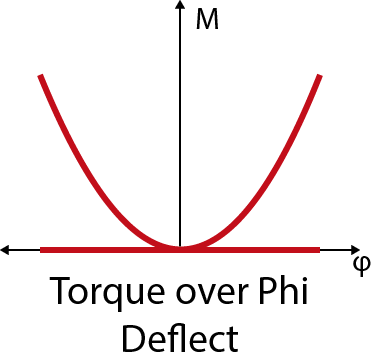
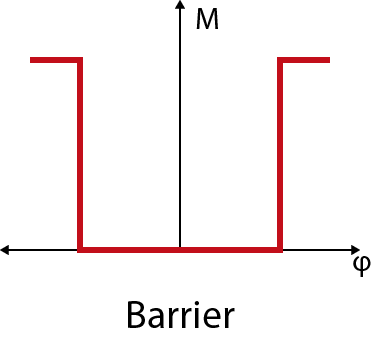
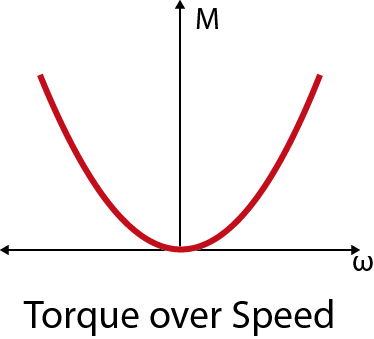
Active steering torque
Increasing steering torque from <0,1 Nm to 8 Nm
The test setup shows an INVENTUS SbW hybrid system in freewheeling mode (< 0.1 Nm) followed by a continuous increase of the steering torque up to 8 Nm, the maximum active torque for comfortable and controlled steering maneuvers.
Max. braking torque
Barrier torque of 25 Nm (up to 35 Nm)
By combining a small electric motor and our patented MR braking technology, we achieve a maximum braking torque of up to 25-35 Nm, as demonstrated by the test setup with a distinct end stop.
Fail safe – functional safety to ISO 26262
Functional safety is of high importance for all steer-by-wire systems.In order to ensure a proper and safe operation of the INVENTUS SbW FFA hybrid system even in case of an incident, two fail safe options are available:
Option 1 – Battery solution
- We use an additional small battery to generate a failsafe driving torque of 1 to 3 Nm (<1 Watt).
- Unlike conventional SbW solutions based on an electric motor, the INVENTUS system does not require any sensors to detect the direction of rotation.
- This way the INVENTUS SbW system can be operated with just a small battery, accumulator or capacitor over a longer time.
Option 2 – Permanent magnet solution
- We supplement the SbW MR brake with a permanent magnet in the magnetic circuit, generating a magnetic field without any current applied – e.g. 2 Nm failsafe driving torque.
- While normal driving, this permanent torque can be canceled by counter current (-) or amplified by the same current direction (+).
- Our customers confirm that our MR brakes featuring a permanent magnet provide a major safety advantage over other solutions on the market, greatly simplify the safety architecture (in accordance with ISO 26262 and ASIL A to D), and at the same time save costs.
INVENTUS SbW permanent magnet fail safe demonstration setup
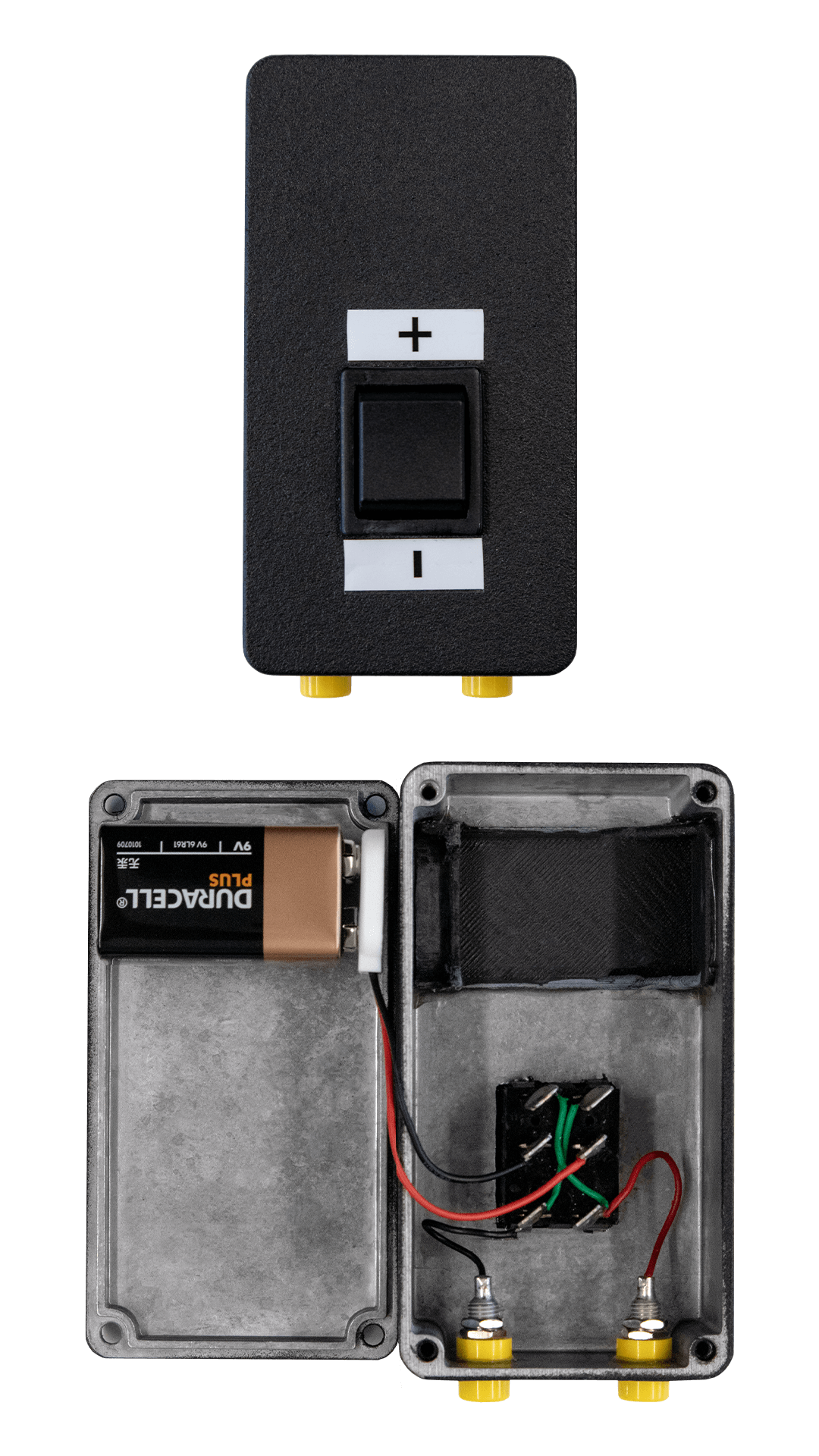
Battery pack with a 9 V battery to demonstrate emergency situations with a permanent magnet fail-safe setup
In normal driving mode (+ button pressed, increased steering torque), the system generates natural steering feedback.
In case of an emergency, the fail-safe drive torque of 1-3 Nm ensures controlled steering maneuvers even without any power supply (no 2nd power circuit required).
Cost savings potential
Due to the simple design of our braking technology, various cost-saving potentials can be utilized
- The INVENTUS MR brake requires significantly less raw materials such as copper, iron and other materials compared to an electric motor with the same torque, which is directly reflected in the manufacturing costs
- The INVENTUS MR brake requires no rare earths
- Also a torque sensor is not essential
- For this reason, we predict the manufacturing costs of the INVENTUS MR brake with 25 Nm braking torque to be in the low double-digit euro range for medium quantities.
- For large quantities, the costs can be in the single-digit euro range.
By combining a MR brake and an electric motor in our INVENTUS steer-by-wire force feedback actuator the size of the motor can be significantly reduced
The electric motor must generate a 3 to 7 times lower active torque (25 Nm braking – 8 Nm active torque; 35 Nm braking – 5 Nm active torque)
The significantly smaller motor is not only cheaper, but also all related components, including cable cross-sections, connectors, ECU components (MOSFETS, shunts, H-bridges, power filtering, etc.) can be optimized for this efficient SbW solution.
Similarly, the redundant/double winding of the electric motor including double contacts, connectors, cables, etc. can be omitted.
Additionally, the saved installation space is another major advantage, as the INVENTUS Steer-by-wire is substantially smaller than state of the art solutions.
Reference projects
INVENTUS technology is reliable and proven in serial production
In cooperation with automotive OEMs and suppliers, we have already developed SbW FFA setups and successfully evaluated them on test tracks.
Additionally, we were a collaboration partner for the project „Steer-by-Wire with a magnetorheological feedback actuator“ with MdynamiX and the University of Applied Sciences Munich.
Moreover, we developed a magnetorheological steer-by-wire feedback brake for the Institute for Driving Assistance and Connected Mobility (IFM) Kempten.
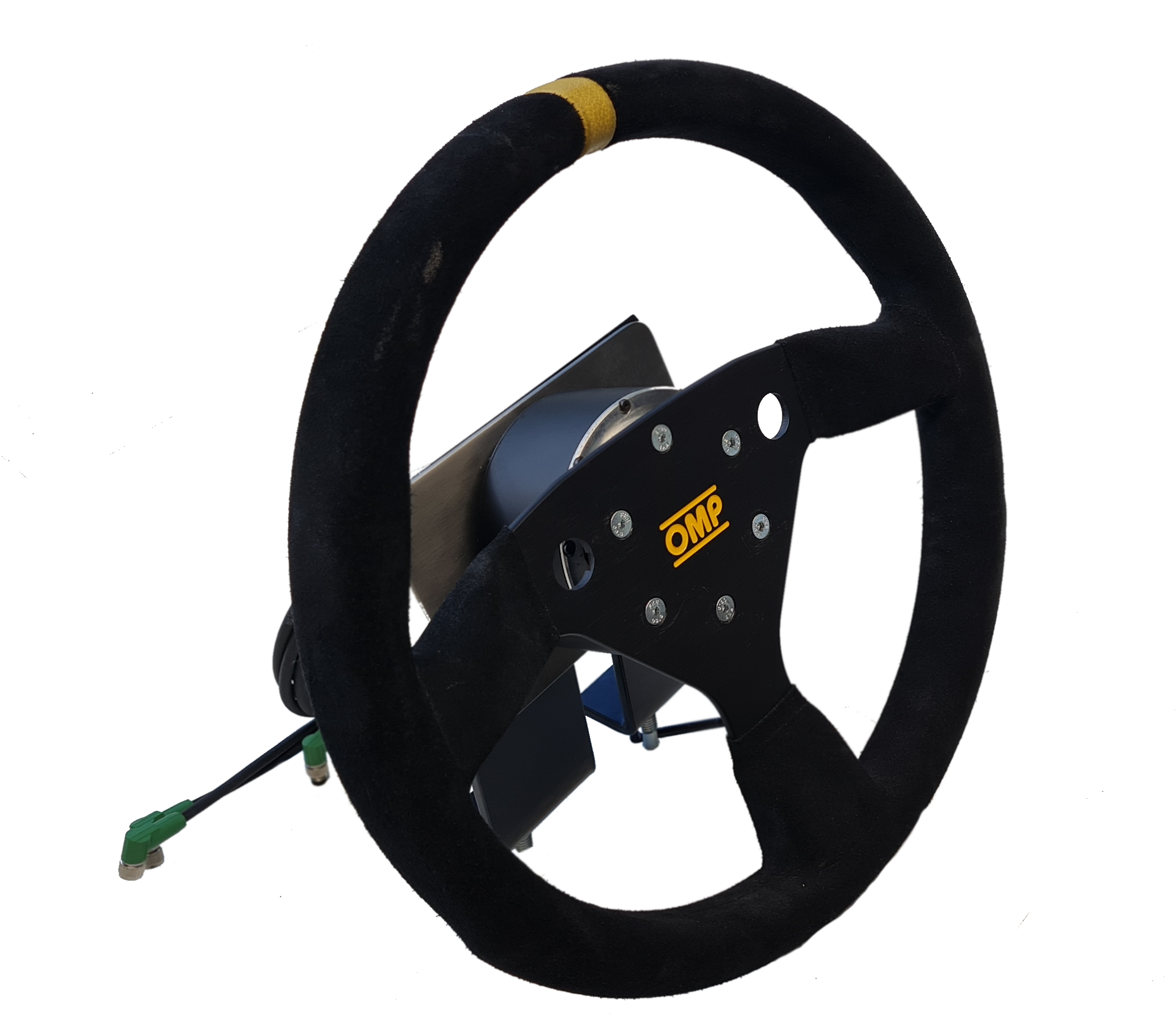
Here you can find the potential analysis a Steer-by-Wire Force Feedback Actuator with Direct Drive E -Motor and MR-Brake.
Presented by Mr. Matthias Niegl at the chassis.tech plus 2024 in Munich
Overall benefits
Key advantages of the INVENTUS MR brake
compared to an electric motor:
- Significantly higher efficiency and power density
- Same performance
- Better steering feedback (force feedback) thanks to lower base torque and absence of motor ripple
- Smaller dimensions / installation space of overall system
- Weight reduction
- Symmetrical system design
- Low power consumption / increased energy efficiency (resulting in potentially higher range for electric vehicles)
- Simple & reliable failsafe setup
- Inhomogeneous redundancy (or hybrid redundancy)
- Cost savings in the double-digit euro rang
